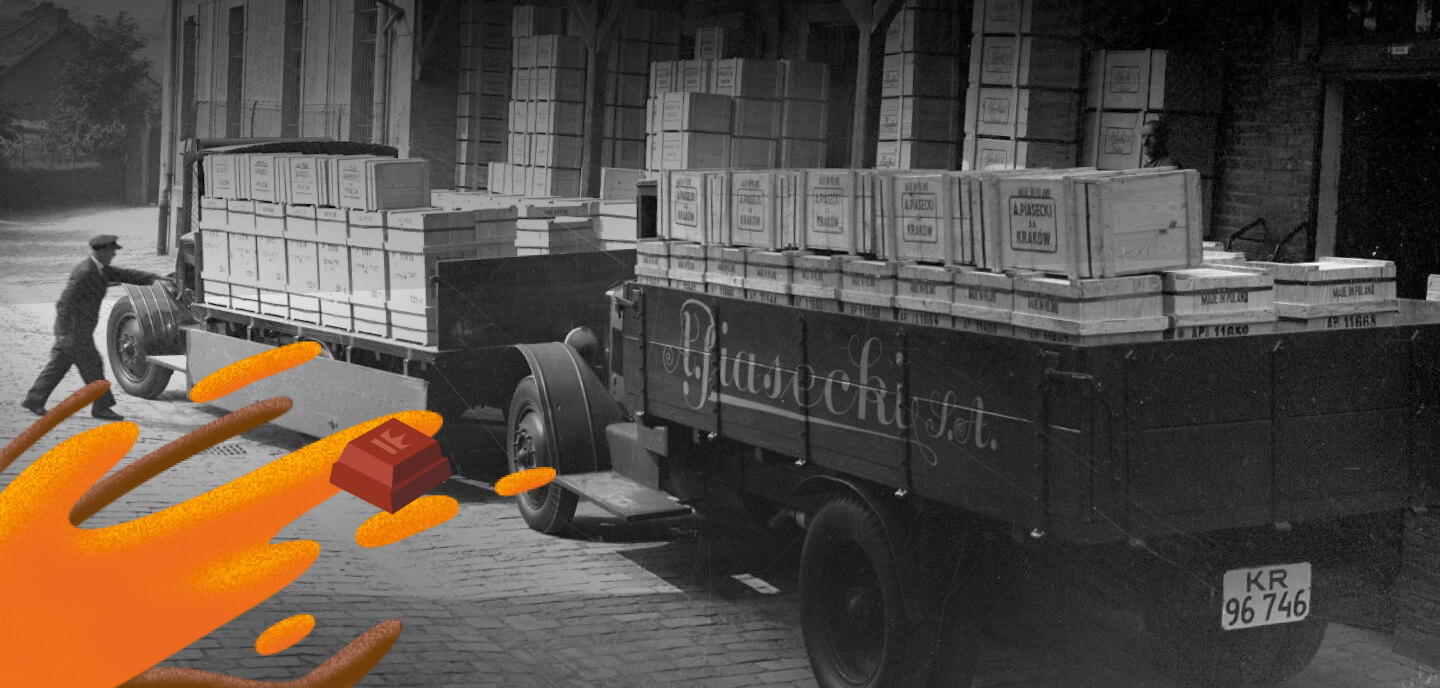
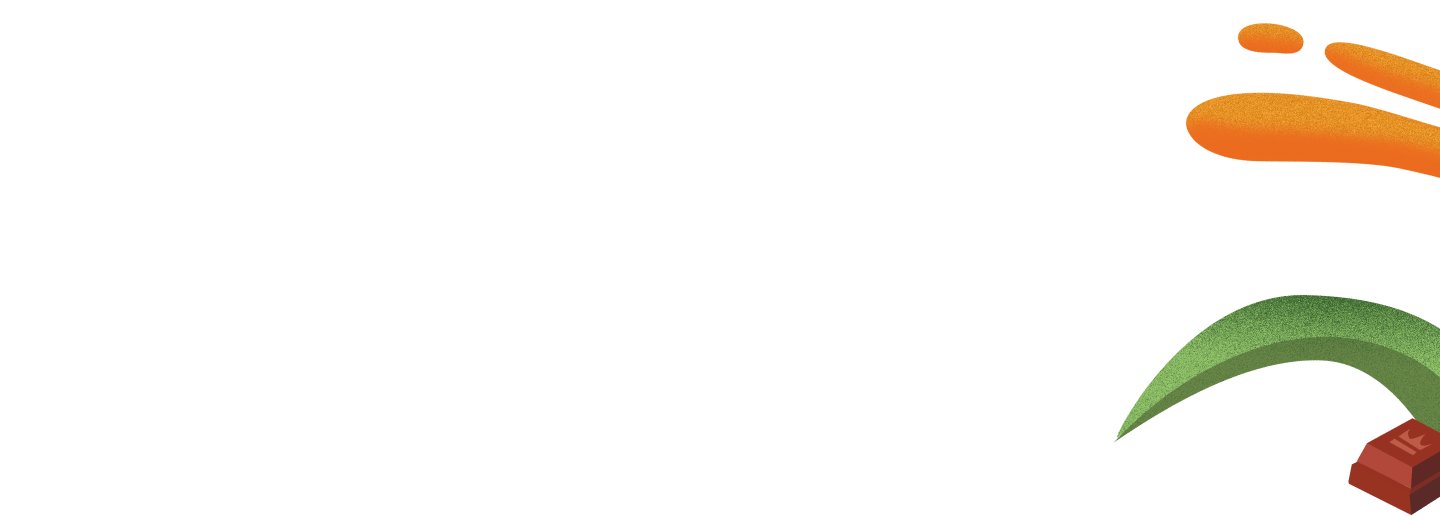
Wawel company and brand history
-
1898
In 1898, young Adam Piasecki, already experienced in his confectionery profession, purchased his first workshop and shop at 20 ul. Długa. This is where the finest sweets in Kraków were soon to be crafted.
-
1910
The increasing demand for products from his confectionery prompted Piasecki to acquire a property at 26 ul. Szlak in the early 1910s. Following the purchase, Piasecki started by adapting the existing structures for factory use and by constructing facilities. By November, the factory was operational and capable of producing 600–700 kg of sweets daily.
-
1914
The “King of Chocolate”, as Piasecki came to be known, along with the Swiss master and a team of 22 employees, dedicated themselves daily to ensuring that their confections delighted even the most discerning palates. Each day, 1,500 kg of the highest quality products, elegantly packaged, rolled off the production line.

-
1918
At the peak of success in the 1920s, Adam Piasecki developed a unique recipe for the renowned chocolate with praline filling, naming it Danusia in honor of one of his employees. Soon everyone wanted to taste how the famous Danusia tastes…
-
1951
In January, the “Wawel” Confectionery Manufacturing Plant was established, experiencing rapid growth under the guidance of top confectioners and advisors. The first chocolate innovation to emerge was Malaga, still cherished today and initially crafted by hand. The Tiki Taki and Kasztanki chocolates, now produced by Wawel using specialised machines, followed shortly after. At the inception of this venture, “Wawel” Confectionery Manufacturing Plant boasted an array of offerings: 36 varieties of caramels, 24 varieties of chocolate collections, 12 hard chocolate varieties and 8 varieties of pastry. Each facility specialised in manufacturing distinct sweet categories, driving down costs, amplifying total production and broadening the range of products at the same time.
-
1960-1980
During this time, Wawel confectionery was produced in three Kraków-based facilities. Each of them is renowned for unique specialisations and products. The first one was located on ul. Wrocławska and mainly produced filled chocolates, and chocolate sweets and bars. Solid chocolate bars and chocolate bars with additional ingredients, chocolate caramels and cocoa came from the facility on ul. Masarska. The beloved Michałki and wafers were churned out daily by the third facility, situated on ul. Kącik.
-
1992
The following years were a period of dynamic development of the company. In the context of economic transformations in Poland, the decision was made to privatise the enterprise and transform it into a joint-stock company – Zakłady Przemysłu Cukierniczego Wawel SA.
-
1997
The Securities and Exchange Commission admits the company’s shares to public trading. The shares of ZPC Wawel SA debut on the main market of the Warsaw Stock Exchange on March 11, 1998.
-
2005
After several years of functioning on the stock exchange, the company changes name to Wawel SA.
-
2006
After more than a century of operating in Kraków, the three plants were consolidated into a single modern production facility constructed in Dobczyce, near Kraków, where the entire production process is gradually being transitioned. Spanning nearly six hectares, this modern factory is situated within the Industrial Zone. The company’s management board headquarters remains in Kraków, situated at 14 ul. Władysława Warneńczyka.
-
2008
Wawel is a company that has never been indifferent to its neighbourhood. The idea of charity has always been deeply rooted in the brand’s philosophy, which is why the “Wawel z Rodziną” Foundation, which continues the company’s charitable activities, was established in June 2008.
-
2015
The plant in Dobczyce is being successively expanded in 5 stages. Wawel produces nearly 45,000 tons of sweets annually, but it does not stop developing. 2015 began the construction of manufacturing plant no. 2 along with the installation of new, ultra-modern production lines and packaging machines. The project, carried out within the Special Economic Zone, is expected to significantly increase production capabilities and enable the manufacturing of new product ranges.
-
2017
The construction of the state-of-the-art manufacturing facility no. 2, connected to the existing one by a technological flyover, has been completed. The new facility is equipped with renewable energy sources (cells providing hot water for domestic and technological use). Despite the clear advantage of ultra-modern machines, there is a place in the Wawel confectionery factory where time stands still. It is the caramel workshop, where original caramels are manufactured with traditional methods from over a century ago, using machines transferred from the old Wawel plants. The Wawel factory meets all the standards required for food manufacturing. The production process is based on proven recipes, and the raw materials undergo meticulous control. This is evidenced by the implementation of a certified quality management system compliant with ISO 9001:2000, a Hazard Analysis and Critical Control Point (HACCP) system compliant with the Codex Alimentarius, the international food safety standard (BRC) and IFS Food (International Featured Standards). Wawel is a responsible manufacturer, caring for its environment and the local community. The factory has high-quality systems in place to prevent the uncontrolled release of pollutants into the environment, reduce noise emissions and minimise water and energy consumption, making the facility environmentally friendly.
-
2023
Today, we still uphold the principle that people are paramount at Wawel. It is thanks to the team’s dedication to crafting products of royal quality that the company continues to thrive. In 2022, approximately 1,000 individuals were employed at Wawel SA. By prioritising employee well-being and implementing solutions that enhance both work quality and life satisfaction, we foster their contentment and instil a greater sense of security.
Despite its systematic investment and development, Wawel is always mindful of the environment. We therefore continuously monitor our potential environmental impact by, among other things, taking control measurements of pollutants emitted into the atmosphere, registering accidents affecting the environment, measuring noise, controlling wastewater parameters and monitoring water consumption/wastewater discharge volumes and recording the amount of packaging placed on the market together with the products.